Build strong, smarter, and greener foundations with StopDigging
Enduring stability for every project
Achieve stability and sustainability without extensive excavation or excess concrete
In construction, laying a stable foundation is critical – but it doesn’t have to come at the expense of solely extensive excavation, high concrete usage, or heavy machinery. StopDigging’s ground screw system offers a smarter and more sustainable solution for concrete slab under-piling. The ground screws provide unmatched stability and load-bearing capacity, even in challenging conditions such as soft soils, sloping terrain, or frost-prone regions. Ideal for both residential and industrial projects, ground screws anchor foundations deeply into stable soil layers, reducing settlement risks and environmental impact.
Complete foundation solution from start to finish
At StopDigging, we provide under-piling solutions for concrete slabs, an efficient alternative to traditional piling methods. Our all-in-one service ensures every step is covered—from precise load-bearing calculations to the professional installation of ground screws. Focusing on durability and environmental responsibility, we provide solutions that reduce excavation, minimise waste, and streamline project timelines.
StopDigging’s commitment to quality and sustainability – Backed by ISO Certification
At StopDigging, we are committed to the highest standards of quality, sustainability, and efficiency in everything we do. Our ISO certifications are a testament to this dedication, ensuring that our products, processes, and services consistently meet international standards.
Our ISO Certifications
Material | EN 10027-1:2016: S235 JR |
Product CE | EN 1090 |
Galvanization | ISO 1461:2009 |
Manufacturing process | EN 1090 / ISO 9001:2015 |
Installation process | ISO 9001:2015 |
Ground screws for concrete under-slab piling foundations
Our heavy-duty SGC and SGX ground screws are designed for superior performance in concrete under-slab piling. Precision-engineered for diverse terrains, they offer unmatched durability and flexibility in demanding environments. Manufactured from high-quality and hot-dip galvanised steel, they ensure corrosion resistance and long-lasting reliability with a minimum service life of 125 years.
SGC adapter screw
Offers exceptional adaptability and load capacity, making it ideal for medium to heavier, demanding structures, and can be used for a wide range of soil conditions.
Product details
- Compression capacity: Up to 91.5 kN
- Tensile capacity: Up to 65 kN
- Lateral capacity: Up to 24.5 kN
- Available in lengths up to 3500 mm
SGX adapter screw
An extendable screw engineered for medium to higher loads. The SGX is ideal for projects requiring additional stability or challenging ground conditions, as it can penetrate deeper into stable soil layers.
Compression capacity: Variable, depends on length
- Tensile capacity: Variable, depends on length
- Lateral capacity: Variable, depends on length
- Available in lengths from 2000mm and beyond
More information about all our ground screws and adapters
Swedish design
with a commitment
to sustainability
All of our ground screw products are designed and developed in Sweden, embodying Swedish precision and high standards of quality, durability, and environmental responsibility.
Comparing ground screws to other piling methods
When comparing ground screws for concrete under-slab piling to traditional concrete slabs without pile reinforcement or driven piles, ground screws offer significant advantages in efficiency, adaptability, and cost-effectiveness.
Foundation challenges | Traditional concrete slab without pile reinforcement | Driven piles | Ground screws |
---|---|---|---|
Concrete usage and excavation | Extensive excavation and high concrete use. | Often require pre-drilling, excavation, or concrete infill to ensure stability, particularly in soft soils. | Require no concrete or extensive excavation, as they are directly screwed into the ground. |
Cost efficiency | Heavy machinery, multi-stage processes, and longer timelines increase expenses. | Longer piles require heavy machinery and potentially higher transportation costs. Additional costs arise from concrete and soil disposal. | Streamlined installation reduces labour, materials, and equipment costs significantly. |
Installation speed | Requires curing time with heavy machinery, and longer construction periods. | Installation involves heavy machinery. Requires extensive setup time. | Rapid installation with minimal equipment; ideal for time-sensitive projects. |
Material efficiency | Heavy reliance on concrete and extensive soil excavation. | Require longer lengths and additional materials. | Reduced material usage while maintaining structural strength. |
Adaptability to terrains | Often requires additional soil treatments, levelling or reinforcements. | More challenging in rocky or irregular terrains, requiring specialised equipment or techniques like pre-drilling. | Handles varied terrains easily; extensive soil stabilisation or levelling is unnecessary. |
Load bearing and tension resistance | Large load bearing in all directions, but at a high economical and environmental cost. | Primarily designed for compression loads, tension resistance often requires additional anchoring methods. | Strong load capacity with natural tension resistance, suitable for high winds and seismic activity. |
Noise and vibration | Significant noise. | Installation involves significant noise and vibrations from heavy machinery, causing potential disruption. | Quiet, low-impact process; minimal disruption to surroundings or ecosystems. |
Environmental sustainability | Large use of carbon-heavy concrete, moving material and heavy equipment. | Generate more waste (e.g., excess soil, concrete), and the installation is more intrusive to the environment.
Not reusable due to their permanent nature. |
Leaves a smaller carbon footprint, as they avoid concrete and require less material. Easily removable and reusable, causing minimal disturbance to soil ecosystems and groundwater flow. |
Case study
StopDigging ground screw foundation system keeps multi-unit project on track
Background
Client need: Establishment of solid foundations
The residential development in Ranui, West Auckland, New Zealand, features two multi-story blocks, each containing six units. This project transformed a site previously occupied by standalone houses. To address ground condition challenges and establish solid foundations for the new structures, the client engaged our partner, StopDigging Ltd, seeking a cost-effective and reliable solution to avoid expensive interventions.
The challenge
Challenges with the ground conditions
Ground condition issues arose that required deeper foundations and additional support at specific points to handle the loads. Standard slab-on-grade was initially planned, but on-site conditions necessitated a different approach. The initial solution involving soil removal and reinforcement with concrete and steel would have significantly increased costs and introduced complexity. Addressing these issues efficiently was crucial to keeping the project timeline on track.
The solution
A CodeMark-certified ground screw foundation
StopDigging provided a CodeMark-certified ground screw foundation system to mitigate ground condition challenges without extensive groundwork.
By working closely with the engineers, StopDigging NZ Ltd customised a solution by determining the load requirements along vital structural points and testing the ground using static pile tests. For areas requiring specific point loads, additional screws were grouped strategically to provide enhanced support.
The results
Significant reduction in installation time and complexity
The project saw a significant reduction in installation time and complexity. This streamlined process allowed for swift construction progress.
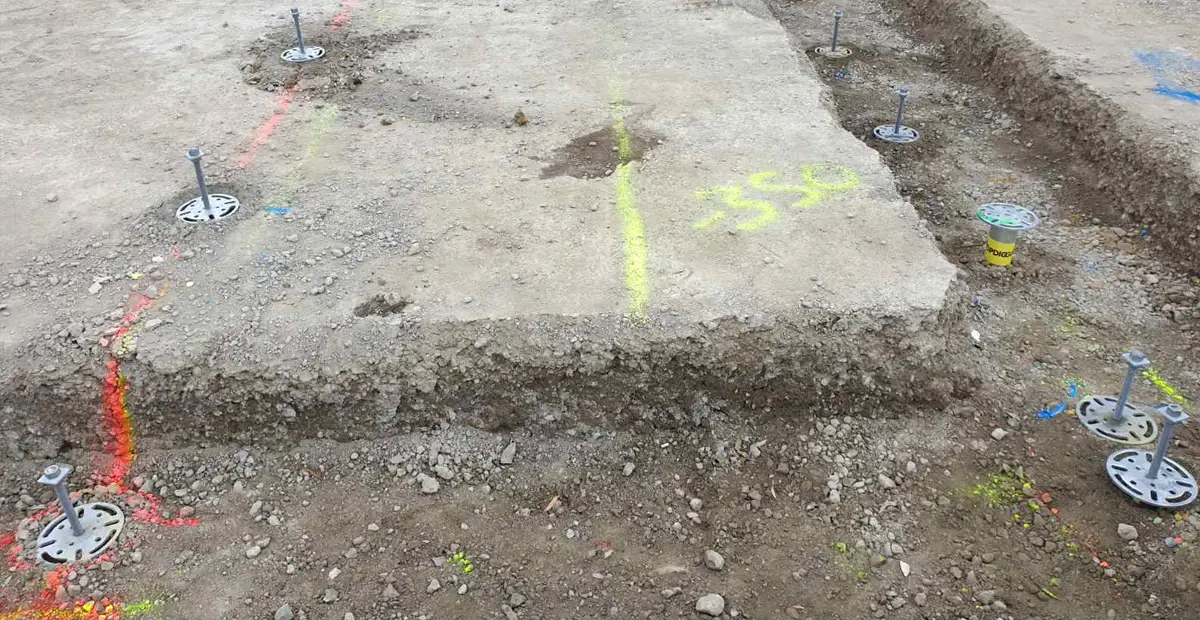
The ground screws were installed in a single day per unit, spread over three days, with 20 screws embedded to a depth of three metres.
The ground screw system eliminated the need for large-scale soil removal, concrete, and steel, making it a zero-waste solution that reduced on-site emissions and aligned with the client’s sustainability objectives.
Client feedback
The engineering team, new to the StopDigging system, recognised its benefits after its implementation. They noted the simplicity of installation and the ease of managing load requirements without significant structural alterations, which have since been recommended for specified future projects.
Get in touch
Are you interested in a quote for your project with our ground screw solutions? Or would you like to work with us? Contact us here for quotes, partnership inquiries, and other questions about your project. We are here to help!
Commitment
to sustainable
foundations
Our solutions are designed with the environment in mind, minimising impact while maximising efficiency. By using ground screws and sustainable materials, we reduce soil disturbance, lower emissions, and adapt seamlessly to various terrains—including challenging sites like steep slopes and remote areas. This approach supports clean installations that respect and protect natural ecosystems, aligning with our commitment to sustainable development.